Proces Manhèsa-Davida
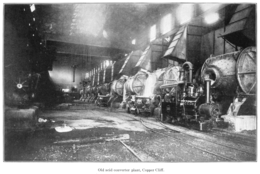
Manhèsa -Davida to proces rafinacji kamieni miedzianych , wynaleziony w 1880 roku przez francuskiego przemysłowca Pierre'a Manhèsa i jego inżyniera Paula Davida [ fr ] . Zainspirowany procesem Bessemera , polega na wykorzystaniu konwertera do utleniania powietrzem niepożądanych pierwiastków chemicznych (głównie żelaza i siarki ) zawartych w kamieniu, w celu przekształcenia go w miedź.
Ilość pierwiastków do utlenienia, a także małe ciepło wydzielane w reakcjach chemicznych , prowadzą do drastycznych modyfikacji konwertera. Manhès i David zaprojektowali go jako poziomy cylinder z dyszami ustawionymi od jednego końca do drugiego. Kilka lat później amerykańscy inżynierowie William H. Peirce i Elias Anton Cappelen Smith wyłożył ją podstawowymi materiałami ogniotrwałymi, znacznie trwalszymi niż te stosowane przez francuskich wynalazców. Chociaż to ulepszenie nie zmienia zasad procesu, ułatwia jego powszechne stosowanie, przyspieszając przejście produkcji miedzi z Wielkiej Brytanii do Stanów Zjednoczonych.
Na początku XXI wieku konwertory Pierce-Smith [ fr ] rafinują 90% kamienia miedziowego i są wykorzystywane w 60% wydobywanego niklu . Ten konwerter, podobnie jak dodatek czystego tlenu, automatyzacja biegu, obróbka dymu i zwiększanie rozmiarów narzędzi, zapewnił trwałość procesu Manhèsa-Davida, nawet jeśli nowoczesne narzędzia mają niewielki związek ze swoimi przodkami.
Geneza procesu
Związek z procesem Bessemera
Tak jak żelazo wytwarzane w wielkim piecu wychodzi stopione z innymi pierwiastkami chemicznymi, takimi jak żeliwo, tak miedź wydobywana z rudy staje się stopem z siarką, żelazem itp. zwanym kamieniem. Zastosowanie tych samych procesów oczyszczania do tych dwóch metali jest zatem logiczne. Zastosowanie procesu Bessemera do metalurgii miedzi zostało zaproponowane i potwierdzone w 1866 roku, dziesięć lat po wynalezieniu Henry'ego Bessemera , przez rosyjskiego inżyniera Semenikowa.
Uszlachetnienie stopu w konwertorze jest możliwe, ponieważ spalanie niepożądanych pierwiastków jest silnie egzotermiczne: utlenianie krzemu i węgla daje odpowiednio 32,8 i 10,3 kilodżuli na kilogram. Z drugiej strony, jeśli kamień miedziowy zawiera dużo żelaza i siarki, pierwiastki te muszą najpierw zostać oddzielone (co zużywa 6,8 kilodżuli na kilogram FeS), zanim rozpocznie się ich utlenianie (które wytwarza odpowiednio tylko 5,9 i 9,1 kJ/kg). .
Pierwsze próby
Pierwsze rafinacje stopów miedzi przez konwertor miały miejsce w Ducktown , Tennessee , gdzie A. Raht pracował nad częściowym rafinacją kamienia od 1866 do 1875. W 1867 Rosjanie Jossa i Latelin próbowali eksperymentalnie zweryfikować badania Semenikowa. W 1870 roku zaprzestali swoich eksperymentów, gdy tylko udało im się zwiększyć zawartość miedzi z 31% do 72-80%.
W Anglii John Hollway kontynuował te próby do 1878 roku. Podobnie jak jego poprzednicy zauważył, że jeśli wdmuchiwanie rozpoczęło się w zadowalający sposób, stawało się coraz bardziej przerywane w miarę postępu udoskonalania. Napotkanych przeszkód było wiele:
- Masa powstającego żużla była równa miedzi, a jego objętość była znacznie większa niż w konwertorze. Dlatego konieczne było regularne opróżnianie retorty .
- Gęstość stopionego metalu znacznie się zmieniła (miedź ma gęstość trzy razy większą niż piryt, z którego jest wykonana).
- Czas trwania nadmuchu powietrza, który może sięgać dwóch godzin, wiązał się z dużymi stratami ciepła.
- Krzemionkowy materiał ogniotrwały został wchłonięty przez żużel, w którym działał jako topnik .
Wszystkich napotkanych trudności nie dało się łatwo rozwiązać: termiczny bilans cieplny reakcji rafinacji miedzi w powietrzu nie był tak korzystny jak w przypadku żelaza, a kamień zastygał w dyszach przed rafinacją . Nawet zmodyfikowany konwerter Bessemera był w stanie co najwyżej usunąć żelazo i część siarki. Hollwayowi się nie udało, ale publikując wszystkie szczegóły swoich eksperymentów, zidentyfikował zasadnicze problemy.
Dysze boczne
W latach siedemdziesiątych XIX wieku francuski przemysłowiec Pierre Manhès rozpoczął swoje pierwsze próby z małym, zwykłym konwerterem Bessemera o masie 50 kg w swojej fabryce w Vedène , następnie w fabrykach w Éguilles , niedaleko Awinionu . Starał się udoskonalić kamień za pomocą 25 do 30% miedzi stopionej wcześniej w tyglu. Ale podobnie jak Hollway, nie udało mu się całkowicie dopracować maty. Utlenianie niepożądanych pierwiastków przebiegało zgodnie z oczekiwaniami, ale działanie szybko zostało zakłócone pojawieniem się metalicznej miedzi. Kamień, który był związkiem jonowym, nie mieszał się z żużlem, ale także z roztopionym metalem. Ta ostatnia, która jest gęstsza (ρ miedź ≈ 9), trafiła na dno konwertera i zatkała dysze.
Następnie Pierre Manhès opatentował zastosowanie dodatków, których utlenianie uwolniłoby wystarczającą ilość ciepła, aby uniknąć utknięcia. W końcu to Francuz Paul David, wówczas inżynier w swojej fabryce w 1880 roku, zaproponował rozwiązanie. Zaproponował poziome dysze umieszczone w wystarczającej odległości od spodu przetwornika, aby miedź mogła się pod nimi gromadzić, a powietrze stale wdmuchiwało w matę. Do 1881 roku ich konwerter był technicznie sprawny i opłacalny.
Jesienią 1884 roku proces ten został przyjęty w Stanach Zjednoczonych przez firmę Parrot Silver and Copper Company w Butte w stanie Montana . Oba typy stawały się coraz większe, zwiększając pojemność od jednej tony do ośmiu ton w 1912 r., A nawet piętnaście ton dla konwerterów cylindrycznych w 1920 r.
Przetwornice Peirce-Smith w fabryce Anaconda Copper w Washoe w 1920 r. Wydajność wynosi 65 ton matowej miedzi, wdmuchiwanej w ciągu trzech godzin (biały metal) + jedna godzina czterdzieści pięć minut (blister). Kształt konwertera jest typu Great Falls.
Ulepszenie przez Peirce'a i Smitha
Ponieważ żużel zostaje wzbogacony tlenkiem żelaza podczas reakcji z powietrzem, staje się zasadowy , a następnie łączy się z krzemionkową wykładziną ogniotrwałą, która jest bardzo kwaśna . Podstawowa wykładzina ogniotrwała nie reagowałaby, a zatem obniżyłaby koszt produkcji. Hollway zasugerował zastosowanie podszewki inspirowanej podszewką opracowaną przez Sidneya Thomasa i Percy'ego Gilchrista w 1877 roku podczas swoich ostatnich testów na początku XIX wieku. Jednak pomysł nie został przetestowany, ponieważ podstawowe problemy związane z nadmuchem powietrza były większym problemem niż optymalizacja materiałów ogniotrwałych.
W 1890 r. pod kierunkiem Hermana A. Kellera przetestowano podstawową wykładzinę ogniotrwałą na jednym z konwerterów Manhès-David firmy Parrot Smelter w Butte. Testy nie dały wykładziny przystosowanej do eksploatacji przemysłowej. W 1906 roku Ralphowi Baggaleyowi, jeszcze w Montanie, udało się, po wielu testach, uprzemysłowić podstawową powłokę w Pittsmont Smelter, którą porzucono w 1908 roku po opuszczeniu przez niego fabryki. Po tym wszystkim Norwegowi Kudsenowi udało się od 1908 roku zastosować podstawową powłokę w kopalniach Sulitjelma . Przeprowadził tam dwa kolejne nadmuchy, najpierw w małym konwertorze z powłoką zasadową, a następnie w drugim konwertorze tradycyjnym z powłoką kwasową.
Wreszcie, w 1909 roku, w hucie Baltimore Copper Company, Amerykanom Williamowi H. Peirce'owi i Eliasowi AC Smithowi udało się rozwiązać główne wady podstawowych materiałów ogniotrwałych; podstawowe materiały ogniotrwałe były bardziej kruche, a przede wszystkim rozpraszały więcej ciepła niż kwaśne materiały ogniotrwałe. Opracowując mur odpowiedni dla cylindrycznego konwertera i zwiększając ilość metalu podawanego do pieca, rozwiązali pozostałe problemy.
Konwerter Peirce'a i Smitha okazał się znacznie bardziej korzystny niż konwerter Manhèsa i Davida. Podstawowy materiał ogniotrwały, który nie reagował z żużlem, wytrzymał znacznie dłużej. Anaconda Copper przypadały dwa konwertery murowane na każdego ). Zmniejszyło to również ryzyko przebicia z powodu słabej kontroli zużycia materiału ogniotrwałego. Warstwa ogniotrwała mogłaby być wtedy cieńsza, zwiększając wydajność konwertera. Wydajność nie była zależna od zużycia materiału ogniotrwałego, co upraszczało zarządzanie przepływami stopionego metalu w fabrykach.
Jeżeli materiał użyty do przygotowania kwaśnego materiału ogniotrwałego zawiera miedź, a nawet srebro lub złoto (często kojarzone z miedzią w kwarcu złotonośnym ), metale te łączą się z matą, gdy podszewka jest usuwana. Biorąc pod uwagę szybkie niszczenie materiału ogniotrwałego, korzyść ekonomiczna kwaśnego materiału ogniotrwałego jest zatem realizowana tylko wtedy, gdy jego zużycie zwiększa wartość procesu. Taka sytuacja jest jednak raczej rzadka i nawet jeśli tak jest, krzemionkę bogatą w metale szlachetne można wytworzyć innymi ekonomicznie opłacalnymi sposobami. Dlatego w 1921 r. podstawowy materiał ogniotrwały uznano za główny czynnik obniżenia kosztów wydobycia rud miedzi. W niektórych przypadkach odnotowano obniżenie kosztów konwersji z 15–20 USD do 4–5 USD.
Konwersja w hutnictwie miedzi
Mieszanina siarczków miedzi i żelaza określana jako kamień jest poddawana obróbce w konwertorach w celu utlenienia żelaza w pierwszym etapie i utlenienia miedzi w drugim etapie. W pierwszym etapie powietrze wzbogacone w tlen jest wdmuchiwane przez dysze w celu częściowego przekształcenia siarczków metali w tlenki:
- FeS + O2 → FeO + SO2 CuS
- + O2 → CuO + SO2
Ponieważ żelazo ma większe powinowactwo do tlenu, wytworzony tlenek miedzi reaguje z pozostałym siarczkiem żelaza:
- CuO + FeS → CuS + FeO
Większość tlenku miedzi jest ponownie przekształcana w postać siarczku. W celu oddzielenia otrzymanego tlenku żelaza do konwertora dodaje się topnik (głównie krzemionkę). Krzemionka reaguje z tlenkiem żelaza, tworząc lekką fazę żużla , która jest wylewana przez pokrywę, gdy konwerter jest przechylany wokół osi obrotu:
- 2 FeO + SiO 2 → Fe 2 SiO 4 (czasami oznaczane jako 2FeO•SiO 2 , fajalit )
Po zlaniu pierwszej porcji żużla z konwertora dodaje się nową porcję kamienia i operację konwertowania powtarza się wielokrotnie, aż do wypełnienia konwertora oczyszczonym siarczkiem miedzi. Żużel konwertorowy jest zwykle zawracany do etapu wytapiania ze względu na dużą zawartość miedzi w tym produkcie ubocznym. Gaz konwertorowy zawiera ponad 10% dwutlenku siarki, który jest zwykle wychwytywany do produkcji kwasu siarkowego .
Drugi etap konwersji ma na celu utlenienie fazy siarczku miedzi (oczyszczonej w pierwszym etapie) i wytwarza miedź konwertorową . W konwerterze zachodzi następująca reakcja:
- Cu S + O 2 → Cu + SO 2
Zawartość miedzi w otrzymanej miedzi konwertorowej wynosi zazwyczaj ponad 95%. Miedź pęcherzowa jest końcowym produktem konwersji.